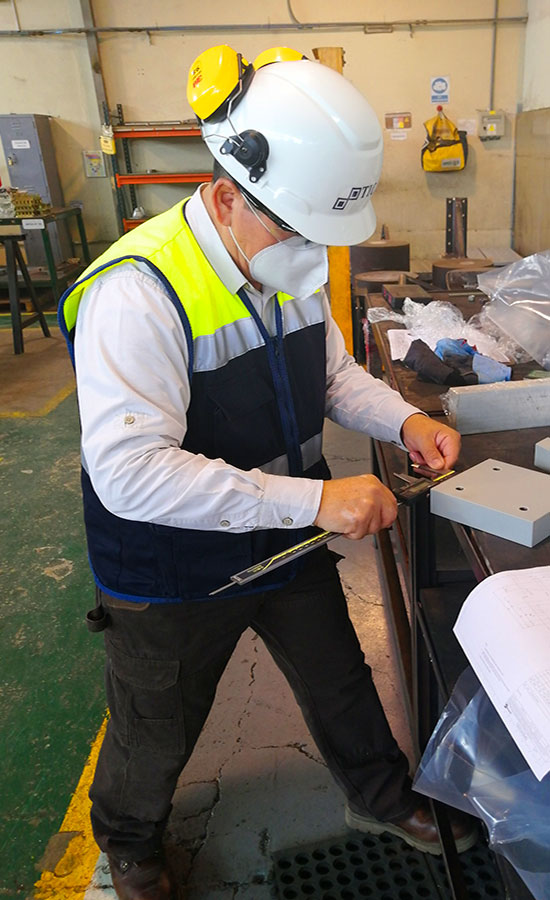
Materials Testing And Non-Destructive Testing
Technological advances in non-destructive testing (NDT)
Non-Destructive Testing (NDT) has undergone rapid technological evolution in recent years, allowing significant improvements in the detection, accuracy and efficiency of tests.
Business Changes and Market Demands
Technological advancements in NDT have led to significant changes in the way companies deliver their services and how customers interact with them:
Customization and Adaptability:
Customers in industries such as mining, construction, and manufacturing demand customized NDT solutions that are tailored to their specific needs, which has led to an increase in the offering of specialized and flexible services.
Augmented Reality (AR) and Virtual Reality (VR) Integration:
The integration of AR and VR into inspection processes could improve data visualization and inspector training, making it easier to identify and analyze defects.
Special Non-Destructive Testing (NDT)
- Conventional Ultrasound, Phased Array, TOFD
- Particulas Magneticas
- ACFM Alternating Current Measurement
- Penetrating Dyes
- Inspection for in-service equipment using B-SCAN RF(TOF).
- Magnetic Flux Leakage (MFL): bottom of tanks, cables and conveyor belts
Destructive Materials Testing
- Mechanical tests (tensile, compression, hardness, flexural impact, Nick Break, Charpy).
- Metallographic tests (Microstructure, grain size).
- Failure analysis.
Analysis and testing of ferrous and non-ferrous materials
- Finite element analysis of materials and equipment
- Chemical analysis of metals.
- Tests on metallic and non-metallic coatings.
- Welding tests.
- Corrosion resistance tests of metal elements and other materials.
- Resistance of materials.
- Mechanical tests on specimens for welding tests.
- Inspection and supervision of paint application, adhesion tests and thickness measurement
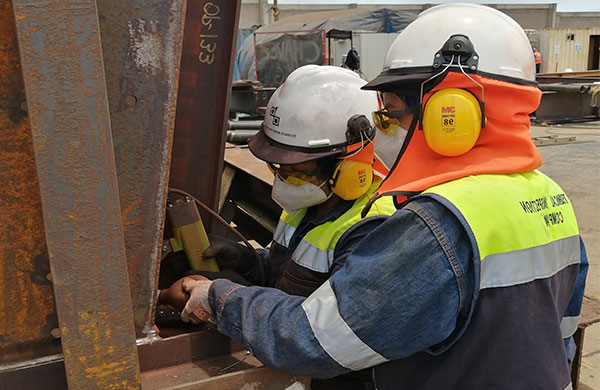
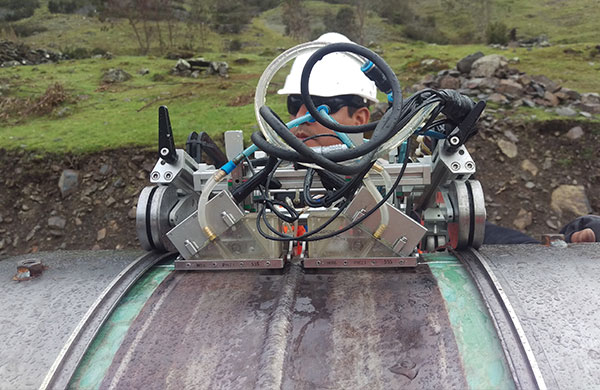
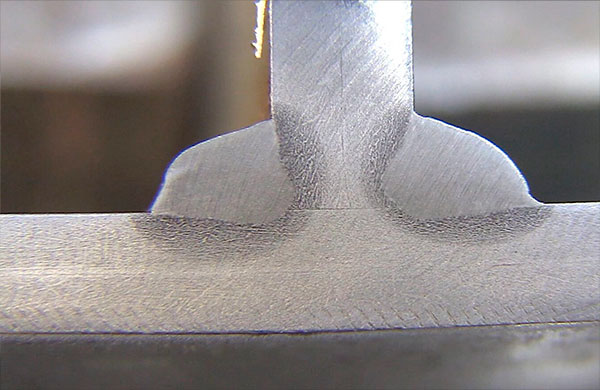
Our service scopes are:
Mechanical and Physical Testing
- Tensile test
- Impact Testing (Charpy, Izod)
- Hardness test (Brinell, Rockwell, Vickers and Knoop)
- Bending and bending test on welded joints and pipes.
- Material fatigue testing on high-wear components.
- Resilience test on low-temperature steels.
- Load and pressure testing on pressure structures and equipment.
- Delamination and adhesion testing on coatings and composite materials.
- Abrasion and wear test on mining equipment parts.
Chemical and Metallurgical Testing
- Salt spray corrosion test and accelerated environment.
- Metallographic and microstructural analysis in steels and alloys.
- Determination of ferrite content in stainless steels.
- Segregation and contamination test in metals.
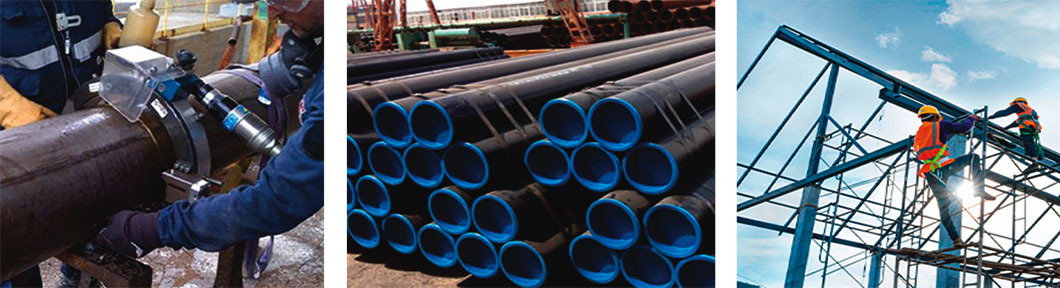
Ultrasonic Inspection (UT)
- Conventional Ultrasound (UT)
- Ultrasonido Phased Array (PAUT).
- Ultrasonido ToFD (Time of Flight Diffraction)
- Ultrasonic thickness measurement
- Detection of internal corrosion and thickness loss
Liquid Penetrant (PT) Inspection
- Inspection of surface cracks in welds and metal materials.
- Detection of discontinuities in stainless steel and aluminum components.
- Testing on critical parts of mining equipment, valves and turbines, etc.
Magnetic Particle Inspection (MT)
- Detection of surface and subsurface cracks in ferromagnetic materials.
- Inspection of structural components and critical welds.
- Evaluation of bolt, gear and shaft failures.
Eddy Current (ET) Inspection
- Tests on heat exchangers, boiler tubes and coils.
- Detection of corrosion, cracks and wear in stainless steel and copper pipes.
- Evaluation of coatings on pipes and structures.
Advanced Visual Inspection (VT)
- Remote inspection with drones for structures at height and hard-to-reach areas.
- Visual borescopic inspection on turbines, compressors and rotating equipment.
- Verification of manufacturing defects in metal structures and electromechanical components.
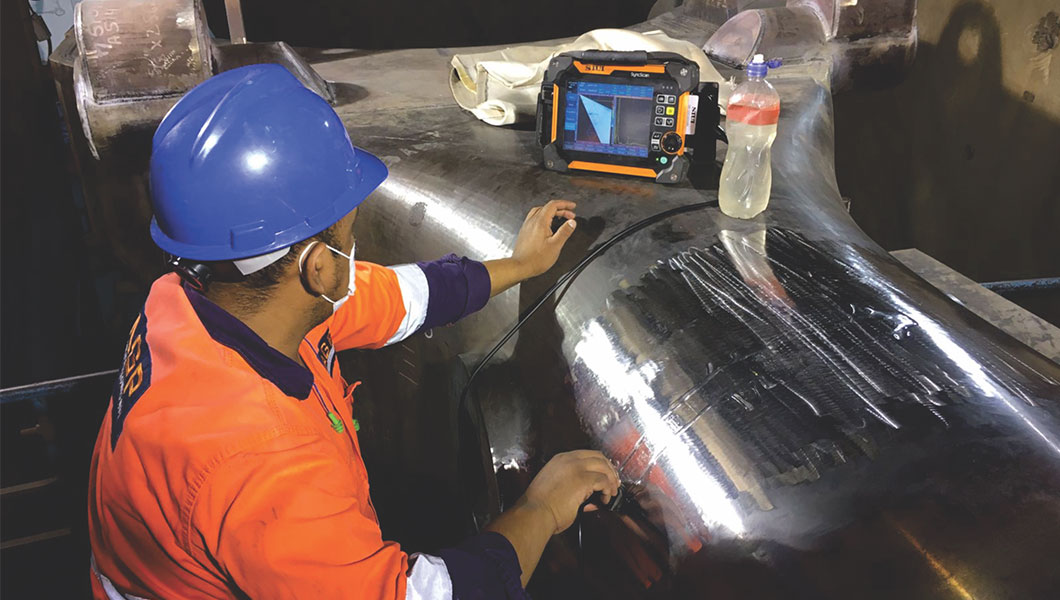
Pressure and Integrity Testing
- Hydrostatic testing on pipes, tanks and pressure vessels.
- Pneumatic testing on gas and compressed air systems.
- Leak and airtightness tests on valves and conduction systems.
Vibration Analysis and Predictive Testing
- Vibration analysis in rotating equipment (pumps, motors, turbines).
- Measurement and diagnosis of imbalance in fans and compressors.
- Condition monitoring of bearings and gears by ultrasound.
Infrared Thermography and Temperature Analysis
- Thermographic inspection of electrical panels and high-voltage connections.
- Evaluation of hot spots in substations and industrial electrical systems.
- Detection of faults in heat exchangers and thermal insulation systems.
Coating and Surface Protection Testing
- Thickness measurement of anti-corrosion coatings and industrial paint.
- Adhesion and cohesion tests in pipe and structure protection systems.
- Chemical and thermal resistance tests on epoxy coatings and polyurethanes.
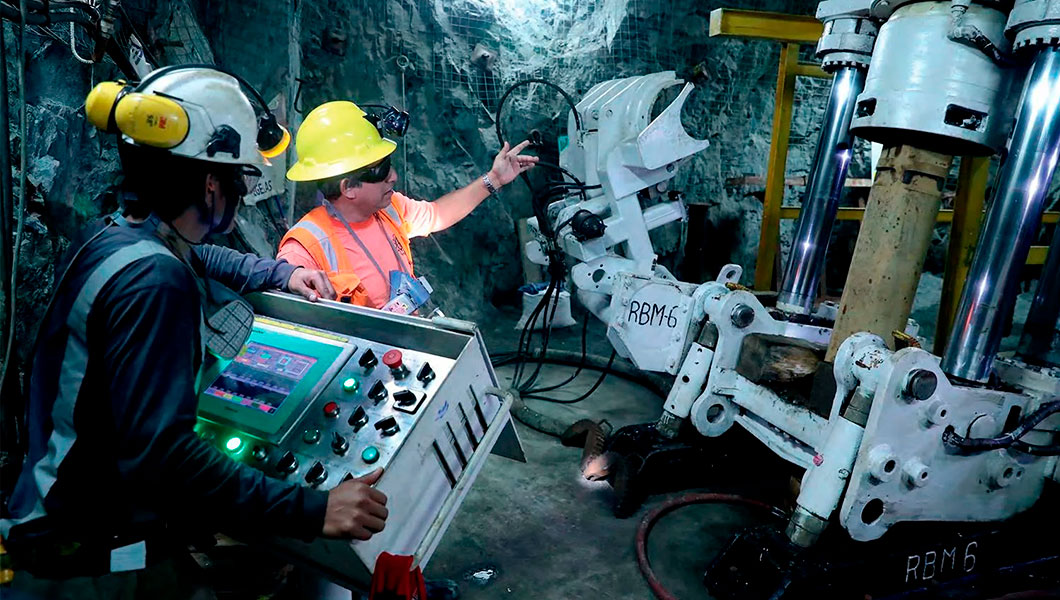